Are you still using PE as the back paint for pipe insulation shells?
- Share
- Issue Time
- Sep 12,2024
Summary
In the pipe insulation project, there are strict requirements for the back paint of the pipe.

In the pipe insulation project, there are strict requirements for the back paint of the pipe.
As the side that directly contacts the pipeline, the paint needs to have temperature resistance, heat resistance, moisture resistance, corrosion resistance, etc.
Each performance of PE is average but not the optimal solution.
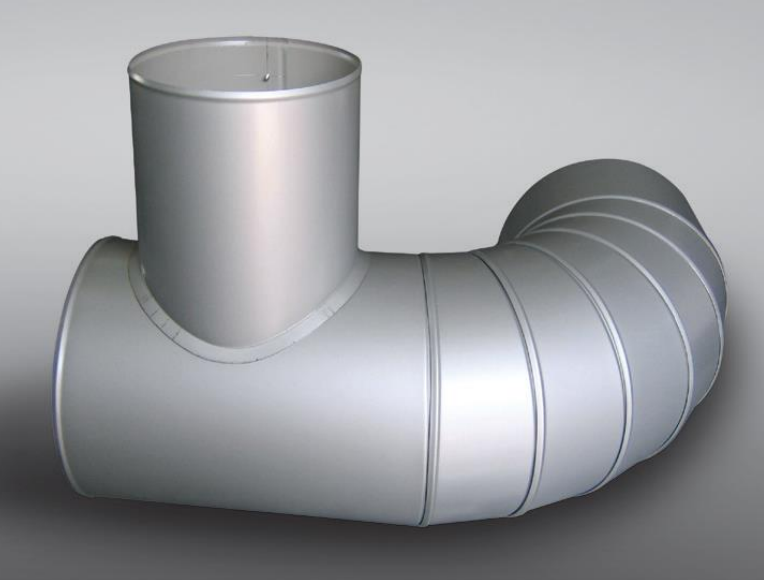
Epoxy paint, as a type of paint that has become increasingly popular in recent years, has been gradually used by 3M in pipe insulation projects since the 1960s.
Compared with PE, epoxy has the following advantages:
1. Heat resistance
Epoxy Coating: Epoxy coatings, particularly epoxy phenolic types, can withstand temperatures ranging from 150°C to 200°C.
Some high-performance epoxy coatings are stable even at temperatures above 250°C.
PE Coating: PE coatings have a significantly lower heat tolerance, typically functioning between 70°C and 90°C, and can soften and degrade at temperatures exceeding 100°C
2. Water resistance
Epoxy Coating: Epoxy coatings has good waterproof performance and performs well in water immersion test.
Usually, under long-term immersion (more than 1000 hours), epoxy coating can maintain 85%-90% adhesion and mechanical properties.
PE Coating: PE coatings has poor water resistance.
In the water immersion test, the performance of PE begins to decline after more than 500 hours.
Water will penetrate into the coating.
If high temperature is applied at the same time, the penetration speed will be accelerated, causing the coating to crack or delaminate.
3. Corrosion resistance
Epoxy Coating: Epoxy coatings are highly resistant to corrosion, especially in acidic, alkaline, and saline environments.
Salt spray tests have shown that epoxy coatings can withstand more than 3000 hours of exposure, making them ideal for aggressive environments.
Coating: While PE coatings are effective in moderately corrosive environments, they perform poorly under prolonged exposure to strong acids, alkalis, or high-salinity conditions.
Salt spray resistance typically ranges from 1000 to 1500 hours
4. Mechanical Performance
Epoxy Coating: Epoxy coatings offer excellent abrasion resistance and impact strength, with hardness ratings typically ranging from 70 to 90 Shore D.
They form a tough, durable layer that adheres well to metal surfaces.
PE Coating: PE coatings are softer, with hardness levels around 50 to 60 Shore D, making them less resistant to mechanical stress, especially in high-temperature or low-temperature environments
Comparison:
Epoxy coatings offer 60°C to 110°C higher heat resistance compared to PE coatings.
Epoxy coatings have superior long-term durability in humid and wet conditions compared to PE coatings.
Epoxy coatings offer 2 to 3 times better corrosion resistance than PE coatings.
Epoxy coatings provide 20% to 30% higher hardness and better impact resistance than PE coatings.
In the pipe insulation project, it is more scientific and reasonable to use epoxy as back paint..
The interesting thing is that POSXX, a large international steel mill in South Korea, also recommends using PE as the back paint when recommending the pipe insulation shell material. This is unreasonable and unprofessional. It seems that they are not as professional in coating design as they are in steel manufacturing.